Challenges
1
Collaboration
Large, complex equipment requiring the collaborative work of multiple Subject Matter Experts (SMEs).
2
Parts Management
Production downtime from poor management and inadequate traceability/tracking of parts from warehouse to maintenance locations.
3
Scheduling & Planning
Multiple moving parts, tools, people and constant change, directly affecting scheduler/planner synchronization and worker coordination.
4
The Human Factor
Lack of communication, inaccurate decision-making, human error and insufficient/inaccurate reporting resulting in costly reworks and delays.
5
Knowledge Loss
Loss of knowledge from personnel migration and lack of documentation or validations on compliance with regulatory standards.
6
Safety & Risks
Increasingly complex equipment and plants, coupled with growing demands for quality, safety and on-time/early job completion, with fewer resources.
7
Uncertainty of Scope
Level of effort, amount of resources and budget required can only really be determined after opening and inspecting the equipment.
Solution
Connected Workers
The Mobideo App provides workers, experts, teams, supervisors, foremen, shop engineers and inspectors with easy access to the most updated information required to complete tasks and provide status updates. Including digital task checklists, forms and granular, step-by-step procedures for execution, automatic sign-offs and hazard notifications where applicable, the application not only tells workers what to do, but also how to do it, enabling them to complete their work using any mobile device.
Read MoreConnected Managers
The Mobideo Control Center turns planned and scheduled equipment overhaul activities into actionable, digitalized tasks, grouped and organized in the correct sequence of execution and automatically dispatched to personnel in real-time, based on the completion of previous tasks or availability to work. It enables the identification, tracking, inspection and testing of tools and parts as they move from the warehouse to the shop floor; provides real-time automated alerts to decision-makers; and delivers complete auditability of who did what, where and when on each task and piece of equipment.
Read MoreProcess Optimization
The Mobideo Optimizer captures all data from the Mobideo App and the Mobideo Control Center, generating a rich data set that is available for immediate BI analysis and for use in real-time digital wallcharts. This valuable data can be used for a range of purposes, such as the compilation of real-time data – including verification of drawings, diagrams, technical specifications and materials used in the overhaul process – into documentation, along with free-form notes and observations. All data is compiled automatically into specific deliverables containing all documents, knowledge, procedures and insights concerning operations/maintenance, which can be transferred to all applicable stakeholders.
Read MoreBenefits
A move from reactive to proactive work culture
Ability to anticipate and resolve issues before they have an impact, and the provision of KPIs to support informed decision-making and shorten shift handover meetings.
Improved safety and more reliable results
Specific digital safety checklists adapted to each task, worker, role and skillset, reducing the likelihood of possibly dangerous safety shortcuts and increasing the reliability of results.
Accountability and traceability
Always know who did what, and when.
Real-time visibility and management of work, better decision-making
Replacement of manual, static, hard-to-maintain, paper-based wallcharts with interactive dashboards and digital wallcharts displaying real-time overhaul status to all stakeholders in any location and facilitating better decision-making based on accurate real-time data.
Immediate, real-time schedule updating
Replacement of painstaking and time-consuming manual scheduling with automated schedule updating, enabling better management of evolving timetables.
Less time wasted on handovers and coordination
Real-time views of actual task execution and immediate understanding of the relevance to dependent tasks, facilitating better coordination of manpower/tools and remote handovers, significantly increasing efficiency and reducing workforce downtime.
Automatic compilation of field data into final reports
Automatic generation of reports in real-time, eliminating the need to manually create reports after work is completed.
Immediate response and resolution of issues/delays based on real-time information
Early, real-time awareness and identification of issues and delays, allowing for improved mitigation as well as driving continuous improvement during the overhaul and supporting improvement in future overhauls.
Streamlined flow of real-time information from discovery to change management
Automated review and approval processes, delivering a frictionless experience with all the necessary digital tools – including images and accurate measurements when anything occurs – eliminating the need for the onsite presence of all stakeholders.
Better resource utilization, efficiency and productivity
Workers can quickly assign themselves appropriate tasks while supervisors can see and allocate available tasks – real-time management based on open lines of communication that can eliminate the time wasted when waiting for instructions or searching for resolutions to problems.
Real-time traceability of tools, rental sign-offs and teams
Reduces the non-utilization of often expensive tools by ensuring immediate awareness of availability for re-assignment, as well as better utilization of NDE teams and tools.
Improved future overhaul planning
The capture and tracking of actual task execution times enables the creation of baselines/benchmarks – rather than estimations – required to perform specific types of tasks for use when planning a future overhaul.
Availability of all relevant data on a mobile device
Real-time access of all relevant and most up-to-date documents and drawings to every user on a mobile device.
Paperless management of the overhaul process with the most up-to-date information
Continuous online updating and pushing of information and detailed digital checklists of procedures to the workforce, ensuring that only the latest, most up-to-date data and best practices for each specific task is accessed, without a single piece of paper.
Learn more about what MobideoSTO can do for your Turnaround.
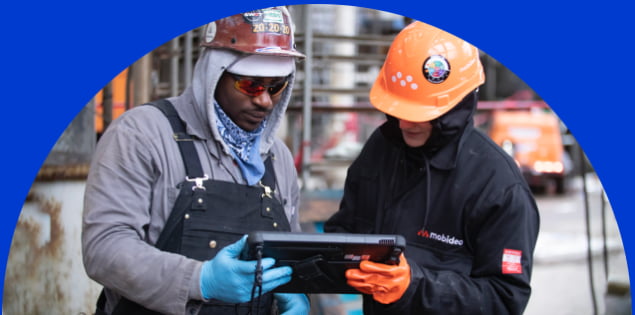