Challenges
1
Communication
Lost productivity from poor communication between crafts/crews working together on a work order
2
Compliance
Work orders in systems of record (EAM / CMMS) remain incomplete or contain missed/skipped activities
3
Productivity
Lack of craft coordination, manual status updates and lengthy shift meetings mean that workers turn wrenches only 30% of the time
4
Visibility
Lack of visibility to work order status and the activities in each open work order
5
Manual Intervention
Extensive effort required to understand work order status and remaining durations
6
Manageability
Challenges to effectively manage resource utilization priorities
7
Siloed Data
Data necessary for decision-making resides in multiple systems of record
Solution
Connected Workers
The Mobideo App enables Maintenance Teams to dynamically populate task content and digital checklists using any mobile device – including the capture and addition of photographs, barcodes and annotations – and push task and work order data and status to the relevant systems of record. This ensures that systems of record are up-to-date, improving compliance and data accuracy.
Read MoreConnected Managers
The Mobideo Control Center turns planned and scheduled maintenance activities into digitalized tasks that are dispatched to teams in the field. Providing alerts and notifications about available work based on the completion of dependent tasks and the prioritization of maintenance tasks, it also enables tracking of progress, the automatic creation of reports, and better decision-making and management of resources, all in real-time.
Read MoreProcess Optimization
The Mobideo Optimizer captures all data from the Mobideo App and the Mobideo Control Center, generating a rich set of reliable maintenance data that is available for immediate analysis and for use in real-time digital wallcharts. This valuable data serves a range of purposes – such as KPI measurement, creation of real-time reports, evaluation of how maintenance tasks are actually being executed and identification of trends and work patterns – that drive continuous process improvement and strengthen operational excellence.
Read MoreBenefits
Less lost time associated to poor communication between task owners/crafts
Significant reduction in lost time associated to poor/lack of communication, both in the field and to the office, eliminating the assignment of tasks before work is ready; the appearance of tasks while predecessor work is still in progress; and unawareness that tasks are available to be worked on.
Real-time visibility and management of work, better decision-making
Real-time, accurate status updates from the field, without the need for paper or duplicate data entry. Replacement of manual, static, hard-to-maintain, stale reports with interactive dashboards and digital wallcharts displaying real-time status to all stakeholders in any location, and facilitating better decision-making based on accurate real-time data.
Improved time on tools
Automated communication between the office and field, as well as between crafts, increasing workforce efficiency, improving time on tools, and providing workers with all the information needed to perform their work in the field.
Enhanced decision making
Collection and contextualization of data from disparate systems of record, providing management with a single source of truth and the ability to make informed decisions based on the full picture.
Timely schedule updates
Improved schedule updating process through the elimination of many manual activities. More timely availability of data direct from the field eliminates the need for schedulers to manually update the schedule, allowing them to focus on their backlog and manage resources. And supervisors no longer have to provide status updates, freeing them to supervise work in the field.
Improved data quality
Status is provided direct from the field, ensuring effective communication, reducing compliance issues and improving data quality in the systems of record.
Optimized shift meetings
Less time spent discussing the status of work (which is already a known), enabling participants to focus on areas for improvement and optimization, and reduce the duration of the meetings.
Less time wasted on handovers and coordination
Real-time views of actual task execution and immediate understanding of the relevance to dependent tasks, facilitating better coordination of manpower/tools and remote handovers, significantly increasing efficiency and reducing workforce downtime.
Better resource utilization, efficiency, and productivity
Workers can quickly assign themselves appropriate tasks while supervisors can see and allocate available tasks – real-time management based on open lines of communication that can eliminate the time wasted when waiting for instructions or searching for resolutions to problems.
Real-time traceability of tools, rental sign-offs and teams
Non-utilization of often expensive tools reduced through immediate awareness of availability for re-assignment.
Improved future event planning
Capture and tracking of actual task execution times replaces estimations with actual baselines/benchmarks – valuable information when planning future maintenance activities, resulting in improved cost and schedule predictability.
Improved vendor management
Understand the total cost of ownership (TCO) associated to a contractor, and not just the contractual rate of payment. Uncover reworks and lost time incidents associated to vendors and use quantitative data to award future work.
Learn more about what MobideoSTO can do for your Turnaround.
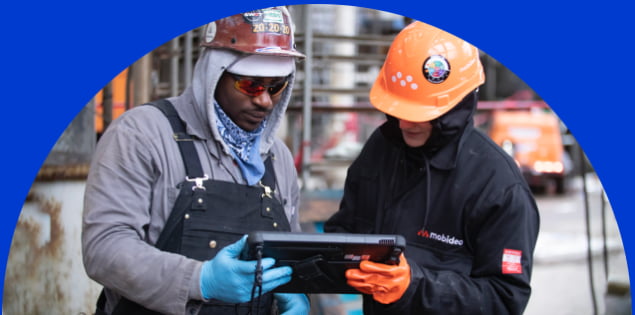